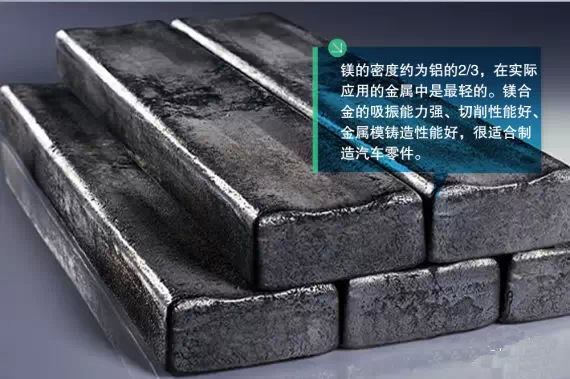
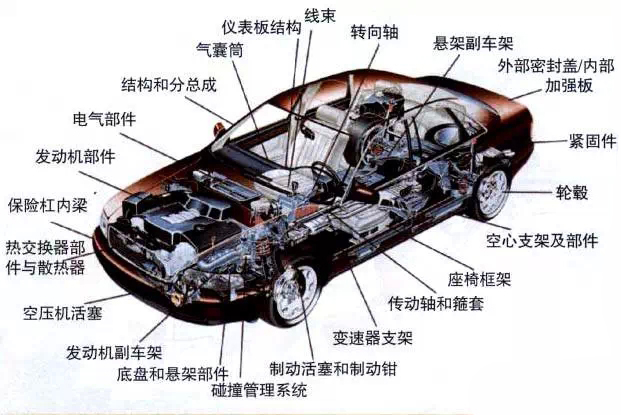
镁在汽车行业的应用由来已久,目前镁合金已在德国轿车上取得成熟应用,在奥迪轿车,已经应用了变速箱壳体、底盘件、手刹、转向支架、踏板架、横梁、顶棚框架等。在奔驰车型上,已应用B系列转向器壳体、CL系列车门内件、变速箱壳体、SL系列油箱盖等。
在我国汽车生产厂家,作为“十二五”国家支撑计划项目的一部分,已研制出自主品牌车型同步开发的变速箱体等8种以上的典型零部件,总重量达到15kg以上,典型零件取样性能达到 σb≥240MPa,δ≥3%并通过相应的盐雾试验和台架试验。瑞麒G6、奔腾B50、东风天锦系列车型亦同步应用,并研制出典型零部件11种,总重量达到30kg以上。除此之外,研制出方向盘、车轮、发动机支架等多项镁合金零部件。
目前,镁合金汽车零部件的研发应用加大与国际先进厂商和研究机构的合作,其中中美加国际合作项目的发起,是开拓镁合金应用的重要一步,该合作项目依托美国密西西比州立大学,建立了中美加MFERD合作项目网络平台,三方共享资源和成果数据。该项目将借助美加设计和测试平台,突破镁合金成形、连接和表面防护等技术,完成防撞性、NVH、疲劳耐久性等多项测试,开发出车神边梁、横梁、减震塔等关键部件,降低前端重量,占领汽车轻量化技术制高点。
目前镁合金在汽车应用上的瓶颈
首先,镁合金的应用面临材料瓶颈,现有镁合金材料存在着一些技术难点:
1.较低的耐蚀性能,受微观结构不均匀性等内在因素,力学/化学交互作用等外在因素的影响,镁合金自身腐蚀寿命较低,现有技术的涂层耐中性盐雾能力可达2000小时,但成本却大幅提高。
2.较低的疲劳性能,受气孔、疏松等铸态缺陷,以及晶粒大小的形变织构等变形组织的影响,镁合金循环变形的行为独特、寿命较低。
3.较低的蠕变性能,受镁合金中β-Mg17Al12等主要强化相热稳定性低的限制,现有镁合金抗蠕变能力处于较低的水平。
其二,镁合金应用问题。
国内现有很多镁合金应用都缺少原创性。以往镁合金应用模式更多的是简单替代和零部件出口,主要是依据用户提供的图纸和样件进行仿造或制造,缺少原创性的中国制造。万丰镁业生产的镁合金卡丁车轮毂占全球市场的70%,都是贴品牌生产,但在国内还没有得到应用。而镁合金与铝合金、钢材等不同材料之间存在着性能差异,镁合金零部件的开发在国外都是从设计开始的。这在国内是个瓶颈。
镁合金应用缺少前瞻性。国外企业在技术上一直沿用“用一代、开发一代”的发展战略,在镁合金集成应用方面做了很多探索性的工作,推出了很多新概念车型,对镁合金应用推广做好了充分的准备。相对而言,我国要么基础研究,要么一步到位的批量生产,缺少投入相对较高、具有前瞻性的应用示范研究。
镁合金应用缺少适用性。在过去的10年中,尽管我国镁合金研究有了令人瞩目的进展,在镁合金新材料开发、成形、焊接和表面处理等单项技术方面具有一定的先进水平,但是,这些单项技术的先进性不足以说明产品制造技术的高水平。实际上镁合金制品的工程化要求的是多项技术的组合,这样的技术体系还需要经过台架实验进行评估,或在整车上经受各种各样的应用考核。
镁合金应用缺少同步性。根据有关数据,近年来主要上市的国产乘用车全新车型共有48款。其中,自主品牌上市的全新款型计30款,远多于外资品牌的18款。这为镁合金应用提供了难得机遇,但遗憾的是镁合金应用并没有能够搭载到这些新车型上,表现出国内整车设计者对镁合金还缺乏深入的了解,镁合金研究者也没有参与到新车型的开发中,致使镁合金应用没有能够与新车型同步增长。
虽然镁合金的应用前景诱人,但镁合金在汽车领域大量应用还需要时间。在当前镁行业需求出现低迷和瓶颈的形势下,需要更理智地看待镁合金未来的应用前景。不因取得应用进展而亢进,也不因应用低迷而低落。首先要充分认识镁合金应用在汽车领域目前的难点和瓶颈,协同应用方共同解决镁合金应用问题,早日在汽车领域实现工程化应用。