摘要
Innovative automotive lightweight designs lead to a higher demand for the product and process development of die cast components. This is attributed to shorter and shorter product development cycles as well as the rising functional integration and complexity of structural die cast parts. The main objectives of the technically complex processes and tools in aluminum and magnesium die casting are cost and resource efficiency along with the robust fulfillment of the defined high-class requirements of the casting. In this context, casting process simulation is a well-established tool used to support tool design, part design as well as process development.
创新的汽车轻量化设计对压铸件的产品和工艺开发提出了更高的要求。这是由于产品开发周期越来越短,以及压铸结构件的功能集成和复杂性不断提高。铝合金和镁合金压铸的复杂工艺技术和模具的主要目标是提高成本和资源效益,并严格满足铸件的高标准要求。在该背景下,铸造工艺模拟是一种成熟的工具,用于支持模具设计、产品设计以及工艺开发。
本文以一个压铸结构件为例,展示了MAGMASOFT ® 5.4自主设计的新方法如何满足压铸的以下需求:
- 更快地开发产品和工艺,
- 在质量、产量和成本方面的最佳工艺和模具设计,以及
- 稳健的工艺布局,比以往更佳的最大化质量再现性。
自主设计通过定义可量化的目标、关键的各种工艺参数和其变量以及相关的质量标准,扩展了铸造模拟的虚拟试验。除可以确定可靠的技术解决方案之外,这种新方法还提供了质量和经济效率之间的最佳折衷方案,这是压铸机一直追求的目标。
可以在没有经济或生产风险的情况下形成系统化知识,使得能够在稳健、经济高效和资源高效的压铸产品和工艺的开发阶段早期做出安全决策。
结构件的开发过程
随着时间和成本压力的增加,各种模型以及激烈的市场竞争导致了产品开发周期越来越短。因此,复杂产品(例如汽车行业的复杂零件)通常只在功能上用虚拟方法(例如CAE)进行设计。关于可行性和潜在可制造性限制的评估会在更晚的时候进行。在此类后期阶段中,很少能够实现合理或必要的设计变更,而且很可能非常耗时且成本高昂。
通过演示部件“接头”和“减震器”的例子,展示了铸造工艺模拟和虚拟优化的系统集成,以确保早期识别产品开发过程中的可制造性限制。接头是从客车车身结构的纵梁到传输管道的碰撞载荷路径的一部分。根据FMVSS,成功的关键因素取决于与系统其他部件的四个计划连接的可行性,以及是否符合正面碰撞的要求,参见图1。
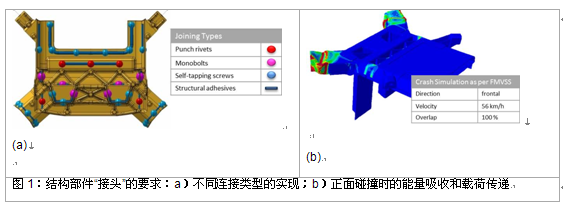
由于几何复杂性和计划产量,选择高压压铸作为生产工艺。铸件功能几何形状的重新设计在常规开发过程的框架内进行。高压压铸的传统设计和结构规则已考虑在内,参见图2。在可能的情况下,通过使用FE模拟工具虚拟验证指定的要求。最终的压铸零件通常会经历运行载荷工况/概要功能要求的相应虚拟验证。通常,在达到设计冻结状态之前,供应商不会参与该过程。
少数情况下,在发送报价请求时,会对可行性进行详细的分析和评估。但是,这通常只在选择了供应商之后才会进行。在供应商方面,工艺开发过程中可行性承诺的稳健性取决于满足铸造要求的能力。在开发工艺布局的过程中,经常会提出或认为有必要进行追溯性的设计变更。但是,在大多数情况下,这些变更只能在一定程度上实现,而且往往耗时且成本高昂。通常,工艺开发以确认供应商可行性和批准生产昂贵的模具和外围资源结束,参见图3。其结果往往是生产工艺不太稳健,透明度低,上升时间长,而且最初废品率往往很高。
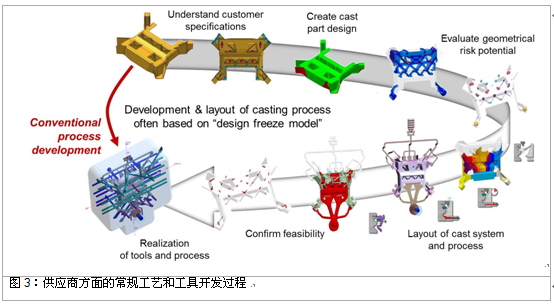
MAGMASOFT ® 5.4通过自主设计为压铸工艺的优化提供了一种新方法和一个包含许多功能的综合工具箱。该软件允许设定不同的目标,评估参数化变量的设计空间,并评估不同的定量质量标准,以确定最佳和稳健的运行条件。通过结合产品开发过程中确定的虚拟功能验证方法,能够在早期分析和考虑制造对铸造属性的影响。这种虚拟生成的知识是自信决策的基础,也为更稳健的产品和生产工艺提供了布局。以下案例研究展示了将MAGMASOFT ® 5.4自主设计应用到压铸零件的整个产品和工艺开发的优势。
总结
在高压压铸中,MAGMASOFT的方法虚拟试验或自主是一种突破性的方法,该方法通过透明和定量的工艺知识,实现模具和生产工艺的优化和稳健布局。除确定可靠的技术解决方案之外,这种新方法还提供了质量和盈利能力之间的最佳折衷方案,这是压铸机一直追求的目标。因此,即使在计划阶段的早期,对于复杂的任务,也有可能生成关于铸件生产参数和质量标准之间相关性的系统知识,而且几乎没有经济或生产风险。
早期的安全决策支持产品开发人员和模具铸造人员设计稳健、经济有效和资源高效的产品和工艺。在规划阶段的早期应用此类虚拟生成的知识是CAE开发过程的基础,在该过程中,设计者和模具铸造者同时对部件和铸造工艺进行优化。